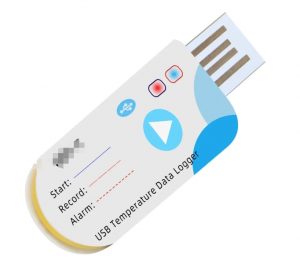
In the realm of cold chain logistics, the integrity of temperature-sensitive products hinges on the precision and reliability of cold chain data loggers. These devices are critical in monitoring and recording temperature data to ensure compliance with safety standards. As a company specializing in PCB assembly and electronic manufacturing, we’ve collaborated with various clients to develop robust cold chain data loggers. This article delves into the essential reliability testing and quality control methods integral to producing dependable cold chain data loggers.
Environmental Stress Testing: Simulating Real-World Conditions
Cold chain data loggers must operate flawlessly across diverse environmental conditions. To validate their resilience, we conduct Environmental Stress Testing (EST) in accordance with IEC 60068 standards . This involves subjecting the devices to temperature extremes, humidity variations, and mechanical vibrations to simulate real-world scenarios. For instance, we expose the loggers to temperature cycles ranging from -40°C to 85°C to assess performance under thermal stress.
Highly Accelerated Life Testing (HALT): Identifying Potential Failures Early
HALT is a proactive approach to uncover potential design and component weaknesses by subjecting devices to stress levels beyond normal operational limits . During HALT, cold chain data loggers undergo rapid temperature changes and vibration tests to identify failure points. This process enables us to address vulnerabilities early in the development cycle, enhancing the overall reliability of the product.
Functional Testing: Verifying Performance and Accuracy
Ensuring that each cold chain data logger functions as intended is paramount. We implement comprehensive functional testing protocols to verify the accuracy of temperature readings, data logging capabilities, and communication interfaces. This includes calibrating sensors and validating data transmission to ensure compliance with industry standards.
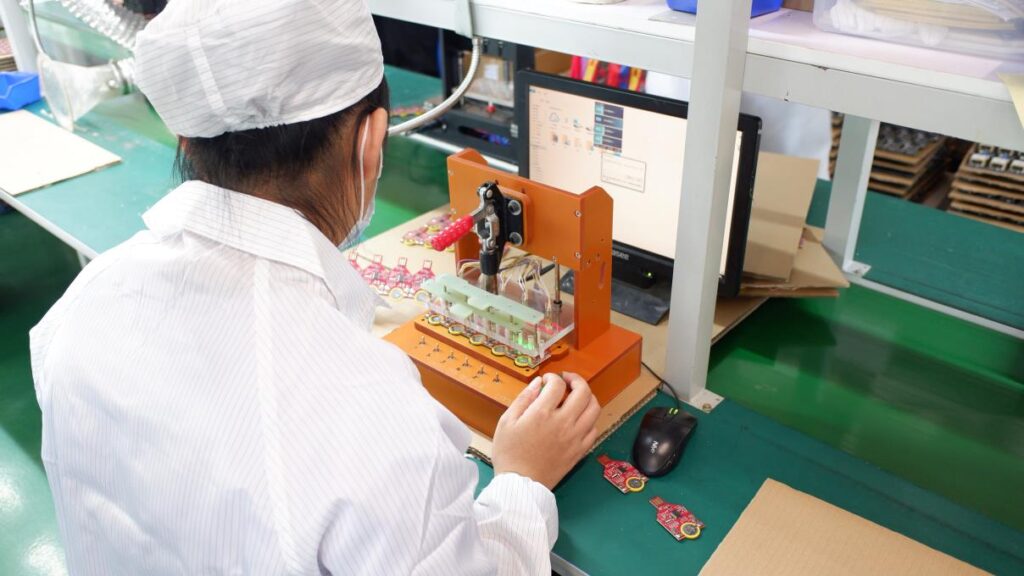
In-Circuit Testing (ICT): Detecting Manufacturing Defects
ICT is employed to detect manufacturing defects such as shorts, opens, and component failures on the PCB. By applying electrical probes to test points on the assembled board, we can quickly identify and rectify issues, ensuring the integrity of the electronic manufacturing process.
Quality Control Measures: Upholding Manufacturing Excellence
Our commitment to quality is reflected in our adherence to stringent quality control measures throughout the PCB assembly and electronic manufacturing processes. This includes:
Automated Optical Inspection (AOI): Utilizing high-resolution cameras to detect soldering defects and component misalignments.
X-Ray Inspection: Examining solder joints and internal structures, particularly for components like BGAs, to identify hidden defects.
Statistical Process Control (SPC): Monitoring production processes to maintain consistency and identify variations that could impact product quality.
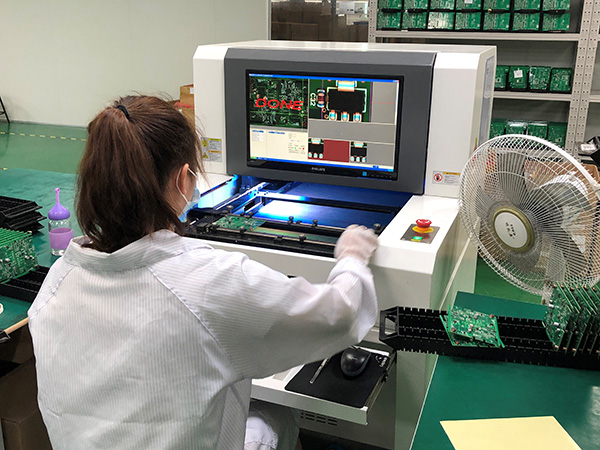
Compliance with Industry Standards: Ensuring Global Acceptance
Compliance with international standards is crucial for the acceptance of cold chain data loggers in global markets. We ensure that our products meet relevant standards such as:
IPC-A-610: Acceptability of electronic assemblies.
CE Marking: Conformity with health, safety, and environmental protection standards for products sold within the European Economic Area.
Conclusion
The reliability of cold chain data loggers is a product of meticulous PCB assembly and electronic manufacturing processes, underpinned by rigorous testing and quality control measures. By simulating real-world conditions, identifying potential failures early, and adhering to international standards, we ensure that our cold chain data loggers perform reliably, safeguarding the integrity of temperature-sensitive products throughout the supply chain.